The Anorak That Was Meant for the Trash
This is the story of our newly launched anorak and how it was actually destined for the trash heap midway through production. It’s also a story about how the textile industry works. Use-and-dispose is bad. Produce-and-dispose is probably worse.
Written by Purchasing and Logistics Manager Eline Guldbrandsen Marchand
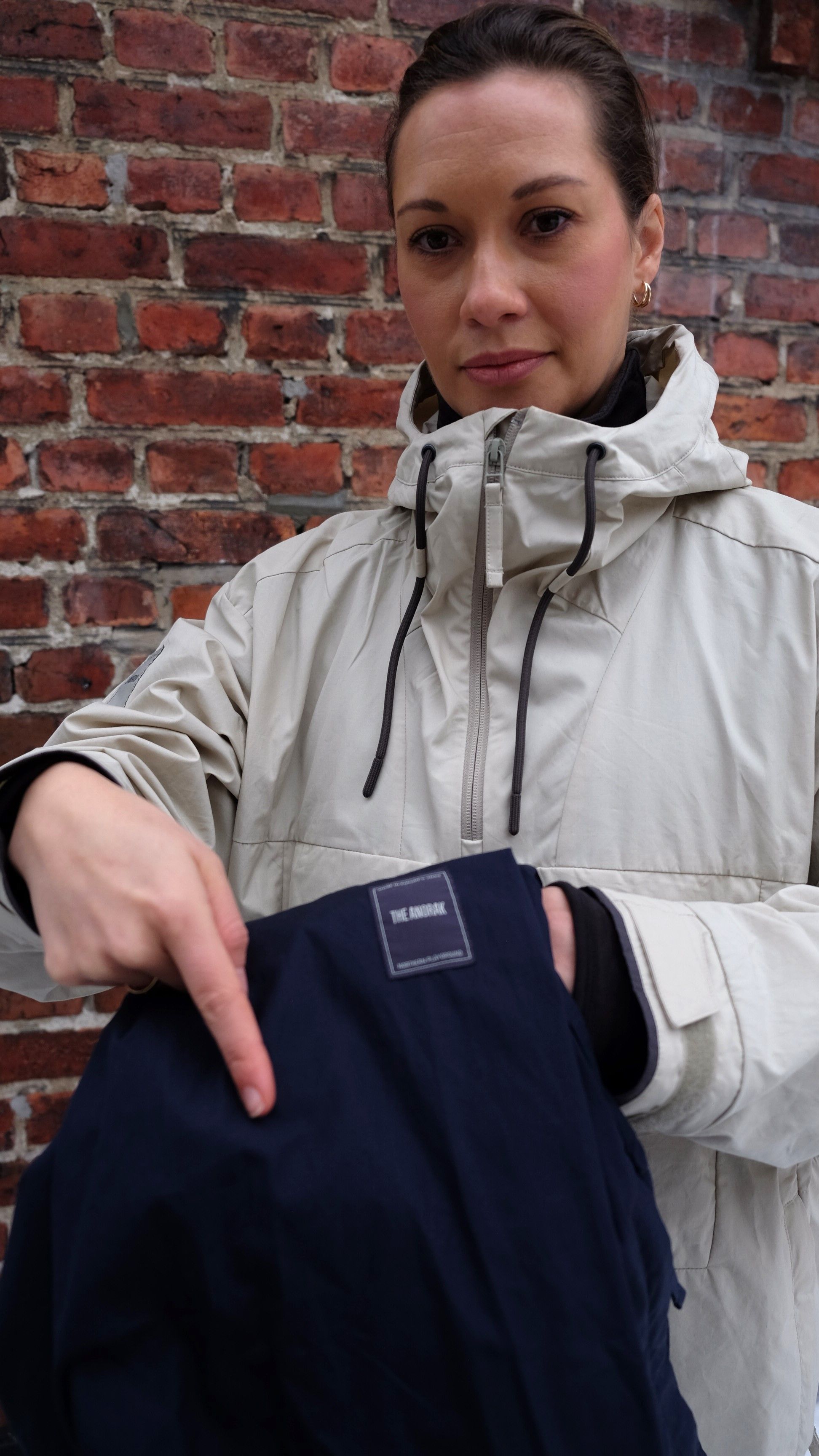
THIN LIGHT STRIPE = TRASH?
When I started at NP a little over a year ago, the team was already deep into designing and testing the anorak made from Ventile cotton. It was meant to be an anorak for all activities, and I especially loved the idea of challenging the aesthetics of cross-country skiing (imagine colorful logos on shiny plastic clothing). The anorak was one of my first products where I took on full responsibility for purchasing and logistics. It was also meant to include a built-in repair kit and many clever little details, so the project was challenging from the outset.
Everything was going well – until it suddenly wasn’t. The supplier responsible for dyeing the fabric had made a mistake. This resulted in some thin stripes with slight color differences appearing here and there on the textiles.
That marked the beginning of a long circus. The supplier refused to approve or deliver the fabric, and quite understandably offered to replace it all and produce a new batch. Hundreds of meters of high-quality cotton were about to be destroyed due to a few minor cosmetic flaws. This was something NP couldn’t live with. Surely, there had to be a way to think outside the box? We asked our manufacturer (LTP) if they could help hide these light stripes inside pockets or similar places. After all, the fabric’s functionality remained completely intact. Unfortunately, this was almost impossible. Computers calculate how to place and cut the different parts from a roll of fabric to maximize material usage. Problem number two was that they, as a matter of principle, wouldn’t approve finished products in their quality control if they had such defects. Hmmm. What to do?
WHAT DID WE DO?
I won’t explain all the details of every dilemma, but I can tell you the outcome. After extensive use of charm, frustration, common sense, and everything in between, we managed to save the fabric and produce (almost) perfect anoraks. It took about three months of delayed negotiations and visual inspections of the entire production, conducted with magnifying glasses by our brilliant designer, Jorunn, and myself in a cold warehouse in Askim. A very small number of products were pulled from sale, but otherwise, you’d need to be Sherlock Holmes to spot the color flaw. You might also like to know that the total cost was a bit lower, so we’ve slightly reduced the price.
We’re very proud of this story. Maybe you’ll find a light spot if you look closely, but it’s really just a scar from an adventure that ended well. And scars, after all, are cool – at least I think so. I hope you agree?
What isn’t so cool is that this happens all the time in this industry. Mistakes are made, and everything is thrown away. Use-and-dispose is bad. Produce-and-dispose is probably way worse.
FIND THE DEFECT
Once in a while, one of the Northern Playground employees sends out a letter giving you an honest look behind the scenes of the company. We believe that transparency is an essential part of being a socially responsible company. This is the 33rd letter. Read the other ones here.