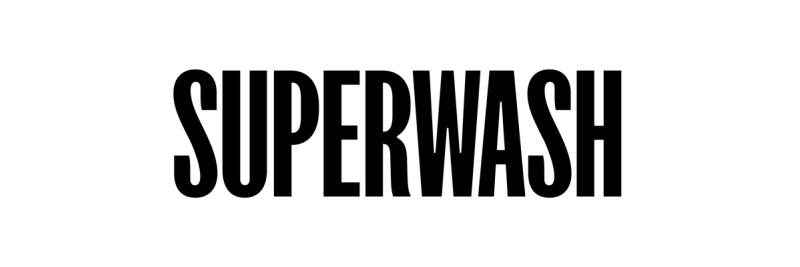
IS WOOL UNDERWEAR REALLY JUST WOOL?
Increasingly, questions are being raised about the actual biodegradability of wool. The reason lies in the treatment wool undergoes on its journey from the sheep's back to your body. To prevent wool from shrinking during washing, it must be treated. The most common treatment involves applying a thin layer of plastic to the wool. This treatment is often referred to as superwash.
Superwash is a process where wool fibers are essentially coated with a thin layer of plastic or synthetic resin. This treatment reduces shrinkage during washing. For a long time, this was regarded as a positive feature, even a mark of quality. However, if this process contributes to microplastics, it is a significant concern. Today, we know that microplastics pose a serious threat to the planet's fragile ecosystems. For instance, fleece products are a major source of the microplastic problem. Research on superwash-treated wool and its subsequent environmental impact is still in its early stages, but there are indications that microplastics from this type of treated wool are released into water systems and negatively affect marine life.
Superwash is only one of the challenges associated with wool treatment. In dyeing and washing wool, manufacturers face a choice between using cheap, environmentally harmful chemicals or more sustainable alternatives. Additionally, chlorine is a part of the superwash process.
WHAT CAN YOU DO?
You will seldomly find how wool is treated (unless it's untreated), so 1. ask about it when buying wool. That doesn't just mean wool underwear, but all kinds of wool products. Use your consumer power to show that this means something to you. 2. Choose products that are untreated or organic. 3. Research, and become a modern consumer that is educated about the products you use!
We fully understand that this makes it even harder to "buy the right thing". The good news is that we see the industry changing every time consumers show they care.
What does Northern Playground do?
Fortunately, alternative treatments for wool exist. In Northern Playground's organic wool and silk collection, the wool undergoes a treatment called Naturetexx Plasma. This process utilizes air and electricity to achieve the same "anti-shrink" effect. Although it is a more expensive treatment, the end result is that the wool remains a pure natural product, and the treatment itself requires less energy. The German company Südwolle developed this process. Read more here.
We hope that further research in this field will clarify the actual environmental aspects of the commonly used superwash treatment.
Below is an article on the topic, written by, among others, Norwegian Kjersti Kviseth.
ANTI FELTING (EASY CARE)
By: Kjersti Kviseth and Dr. Paul Swan
Questions are arising related to the true biodegradability of wool, how wool sheds microfibres, and how anti felting treatment affect biodegradation, specifically in marine environments.
Superwash
Most wool actually is coated in plastic, in nano-thickness layers provided by the Hercosett Superwash treatment. This is not compliant with the natural picture we are communicating about wool.
As Dr. Paul Swan puts it; There is an emerging issue on the links between micro- and nano-plastic pollution in terrestrial and marine environments, and health impacts in ecosystems (including human health impacts) - such links could prove damaging to wool's hard-won reputation as a healthy choice.
600 tonnes of polymer is applied to wool each year for machine wash purpose, 76% of this is Chlorine-Hercosett, where the Hercosett (polyamide-epichlorohydrin) component includes chemistry of known human and eco-toxicity effect (epichlorohydrin). Given the polymers are applied as a thin layer (microns thick), the residues could well pose micro-fibre or indeed nanoparticle risks.
According to Roy Kettlewell, a specialist in the wool chemistry field, Hercosett process stops the degraded proteins on the fibre surface from being washed away during laundry. The degraded proteins swell and help stop the scales from getting close enough to interact and lead to felting. Most of the alternatives to Hercosett rely on inter-fibre bonding to impart shrink-resistance, and this mechanism is not compatible with top processing because of subsequent gilling and combing operations.
Hercosett is classed as BAT [best available technology] in Europe, because it can consistently meet the required standards of washability on all types of wool product. This is a customer requirement and expectation that may be very challenging to change.
Polysiloxane coating
The most widely used alternative to Superwash. A reduction in volume of polymer applied per kg, (0.15% solids vs 1.5-2.0% solids for Hercosett) and a much lower toxicity risk. Process time and cost are its disadvantage.
Mercerisation
The mercerised merino process used to be the most common approach to machine washable wool for many top processors and spinners because it also improved handle for next to skin products. The mercerised merino process is slower and does weaken the fibre slightly, and the overall cost of yarn is 5 to 10% higher than chlorine Hercosett treated yarn. The mercerised merino process uses 2 to 3 times as much chlorine, thus AOX generation is significantly higher and an issue of concern.
Lanazym by Dr.Petry
In the 90's Dr.Petry developed an enzyme based process that complied with Cradle to Cradle principles. This process is less effective in terms of felting than Superwash, and difficult to control during the processing.
EXP by Schöller
A process from the Schoeller Spinning Group that enables the wool to remain machine-washable without the use of chlorine. EXP employs natural salts as an oxidizing agent, as well as an “ecological” polymer for micro patches on the yarn surface. Certified Blue Sign, Ökotex and GOTS.
NaturtexxPlasma by Südwolle
Naturetexx® Plasma is using electricity and air to provide the anti felting effect. The effect is slightly lower than for Superwash. The plasma treatment modifies the surface of the individual wool fibres altering the scales on the fibre surface that cause felting.
It also creates energy savings in the downstream dyeing process. Waterborne dyes are taken up more quickly, and penetrate into the fibre more easily, meaning that the dyeing process can be shortened and less energy is required as a consequence.
The electricity used comes from renewable energy sources. Certified for organic use by GOTS and IVN Best, as well as Bluesign® and OEKO-TEX®.